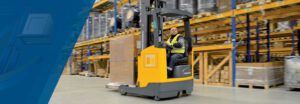
10 Ways to Improve Fleet Utilization
Improving equipment utilization and productivity in a warehouse setting is essential for optimizing operations and minimizing costs. Here are several effective solutions to enhance both:
Fleet Managers are responsible for finding the most efficient method for operating their material handling fleet. They feel pressure to search for and find new ways to make incremental improvements to their operation. It is a difficult task to manage planned maintenance, fleet and operator productivity, and the lifecycle of their forklift fleet. If the fleet is spread throughout multiple locations, the challenge increases. One way to reduce this difficulty is to rely on a lift truck fleet management system. A proper fleet management system should allow you to manage your fleet entirely online by providing full access to fleet data, a way to centralize your service requests and invoices, and provide 24/7 support.
Here are three key benefits you may be missing out on if you are not using a fleet management system:
A forklift fleet management system can help you improve the efficiency of your fleet by keeping you up to date on planned maintenance, a critical component to decreasing equipment breakdowns and limiting costly downtime. A full-featured fleet management system lets you easily manage your planned maintenance schedule for your entire fleet, quickly view the number of PMs completed in the last thirty days and see how many assets are due for PM in the next thirty days.
A telematics device can be attached to your forklifts to provide real-time updates on your fleet. With telematics, Fleet Managers can receive impact and battery monitoring, and review operator access, pre-shift forklift inspections and hour meter readings. You can also set up automated text or email alerts so you’re always up to date on your fleet.
Managing expenses for a large fleet spanning multiple locations can be a top challenge if done manually. Did you spend more money on Accidental Damage or Planned Maintenance this year? By utilizing a fleet management system, you can review the expense mix to see where you spend money and in what service category. And review a year-over-year comparison to see if your ratio of damage to vehicle maintenance has increased or decreased.
A fleet management system that includes a centralized dispatching and invoicing service can help alleviate the pressures of requesting service and managing invoices. A centralized service system will help you ensure that each location receives the same level of service and that billing rates and labor hours are standard across your company. You can easily request service from your local dealer online and receive one centralized bill for all locations (weekly, bi-weekly, monthly, etc.), which can help save you on billing overhead.
It is much easier to make decisions about your fleet when you have access and the ability to review your entire fleet’s data. A fleet management system can help you know when to retire, replace, relocate, or retain a piece of equipment.
It is essential to keep records of your forklift fleet maintenance history and track the utilization rate for each forklift. A forklift utilization rate above ninety percent is typically an indication of an overworked forklift. Compare your utilization percentage to a forklift’s cost per hour, and you can begin to make an informed decision on what to do with the forklift.
Using data to make the most educated decisions about your forklift fleet will help you save time and money while increasing your efficiency and productivity. Using a fleet management system to collect and analyze that data can help you make the most of your forklift fleet in the easiest way possible.
Tri-Lift NJ offers a suite of forklift fleet management software and tools that might fit all your fleet management requirements – Lift Truck Solutions. Lift Truck Solutions’ forklift fleet management software offers a wide array of solutions including:
Click here to contact us and learn more about the capabilities of Lift Truck Solutions.
Whatever fleet management solution you choose, make sure it works for you and your operation. Not sure where to start? For additional guidance on choosing the right forklift fleet management tools, Tri-Lift NJ is always here to help.
Improving equipment utilization and productivity in a warehouse setting is essential for optimizing operations and minimizing costs. Here are several effective solutions to enhance both:
1.Implement Vertical Storage Solutions Maximizing vertical space is one of the most effective ways to increase warehouse capacity without the need for costly expansions. By
732.220.0444
1471 Jersey Avenue
North Brunswick, NJ 08902