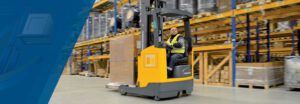
10 Ways to Improve Fleet Utilization
Improving equipment utilization and productivity in a warehouse setting is essential for optimizing operations and minimizing costs. Here are several effective solutions to enhance both:
Improving equipment utilization and productivity in a warehouse setting is essential for optimizing operations and minimizing costs. Here are several effective solutions to enhance both:
1. Conduct Regular Equipment Audits
Regularly assessing equipment usage and performance is crucial for optimizing operational efficiency. By conducting these audits, businesses can identify underutilized assets, revealing opportunities to reallocate or sell excess equipment.
This analysis also helps highlight equipment that requires maintenance or upgrades, ensuring that resources are used effectively. Additionally, the audit can inform decisions about where additional investment is necessary, whether for more advanced technology or for replacing outdated machinery, helping to maintain productivity while controlling costs.
2. Implement a Warehouse Management System
A robust Warehouse Management System (WMS) offers real-time insights into equipment usage, inventory levels, and order statuses, enabling managers to allocate resources more effectively. By providing accurate data on stock and workflow, the WMS enhances decision-making and optimizes the scheduling of tasks and maintenance.
Streamlining workflows and improving order accuracy minimizes errors and delays, leading to better productivity and faster fulfillment. This integrated approach supports smoother operations and helps reduce operational costs by eliminating inefficiencies and improving overall performance across the warehouse.
3. Optimize Equipment Layout
Designing a warehouse layout with efficiency in mind is crucial to optimizing operations. Strategically position equipment, storage, and workstations to minimize unnecessary travel, reduce wait times, and prevent bottlenecks in high-traffic areas. Group related tasks and equipment together to streamline workflows, ensuring that operators can easily access tools and inventory when needed.
This thoughtful arrangement not only improves speed but also enhances safety, reduces worker fatigue, and increases overall throughput, making it easier for teams to meet operational goals effectively.
4. Cross Train Staff
Training staff on multiple types of equipment enhances operational flexibility, enabling managers to deploy workers where they’re needed most. This versatility ensures that operators can step in for each other when necessary, maximizing the usage of available equipment and preventing bottlenecks.
It also reduces downtime, as staff can quickly switch tasks and keep workflows moving smoothly. This approach leads to higher productivity, better resource allocation, and a more adaptable workforce, ultimately supporting a more efficient warehouse operation.
Integrating automated solutions, such as Automated Guided Vehicles (AGVs) or robotic pickers, can significantly streamline warehouse operations. These systems excel at handling repetitive and time-consuming tasks, such as moving goods or picking items, freeing up human workers to focus on more complex, strategic roles that require decision-making or specialized skills.
This division of labor not only increases overall productivity but also reduces errors, enhances safety, and ensures a smoother workflow, ultimately driving efficiency and lowering operational costs.
6. Monitor Performance Metrics
Establishing key performance indicators (KPIs) for equipment utilization and productivity allows managers to measure efficiency and identify areas for improvement. Regularly reviewing these metrics helps uncover patterns, such as underutilized assets or excessive downtime, and provides data for informed decision-making.
By analyzing KPIs, warehouses can optimize equipment deployment, refine workflows, and quickly address inefficiencies. This ongoing evaluation ensures resources are used effectively, improves operational performance, and supports continuous improvement in processes, ultimately leading to reduced costs and increased productivity.
7. Develop SOP’s
Developing standardized operating procedures (SOPs) for equipment use ensures uniformity across operations, reducing the likelihood of errors or accidents. These clear guidelines outline best practices, safety protocols, and maintenance routines, enabling operators to handle equipment efficiently and consistently.
With standardized processes in place, training becomes more streamlined, and workers can easily adapt to different tasks. Ultimately, SOPs enhance productivity by reducing mistakes, minimizing downtime, and ensuring that equipment is used to its full potential while maintaining a safe working environment.
8. Enhance Maintenance Practices
Ensuring equipment is well-maintained through regular inspections, servicing, and repairs helps prevent unexpected breakdowns, reducing unplanned downtime. Proactive maintenance ensures that machinery runs at its optimal performance, avoiding costly disruptions to operations.
By addressing potential issues before they escalate, you not only extend the lifespan of equipment but also boost productivity, as well-maintained machinery performs more efficiently and safely. This approach leads to greater reliability, lower repair costs, and a smoother workflow, all of which contribute to long-term operational success.
9. Invest in Training and Development
Providing ongoing training for staff on best practices for equipment use can significantly enhance operational efficiency. Training should cover key areas such as safe handling, troubleshooting techniques, and methods for effective operation. By educating staff on proper procedures, you reduce the risk of accidents, improve equipment performance, and ensure that employees can resolve minor issues independently, minimizing downtime.
Regular training updates help keep the team informed on new technologies and methods, fostering a more knowledgeable and productive workforce. This investment in training pays off in smoother, more efficient operations.
10. Schedule Downtime Strategically
Planning maintenance and downtime during off-peak hours is a smart strategy to minimize disruptions to warehouse operations. By proactively scheduling maintenance during less busy periods, you ensure that critical equipment remains available when needed most, preventing delays and maintaining productivity.
This approach helps reduce the impact of downtime, allowing staff to focus on core tasks without interruptions. It also enables more thorough inspections and repairs, as there is less pressure to rush, ultimately leading to more efficient equipment performance and longer lifespan.
By implementing these solutions, warehouse managers can significantly enhance equipment utilization and overall productivity, leading to more efficient operations and improved bottom lines. We are here to help! Contact us today!
Improving equipment utilization and productivity in a warehouse setting is essential for optimizing operations and minimizing costs. Here are several effective solutions to enhance both:
Integrating technology into warehouse operations can significantly enhance efficiency, accuracy, and productivity. Here are some solutions to effectively incorporate technology into warehouse management: Implement Warehouse
732.220.0444
1471 Jersey Avenue
North Brunswick, NJ 08902