KEY CHALLENGES and solutions
Managing material handling equipment (MHE) is a crucial yet complex task for warehouse managers, operations managers, and owners, impacting everything from operational efficiency to safety standards. As warehouses grow in scale and demand increases for faster, more accurate order fulfillment, the challenges of maintaining, optimizing, and safely operating equipment have become more pressing.
From handling maintenance schedules and minimizing downtime to managing costs and implementing new technologies, warehouse managers face a range of issues that can disrupt workflow and affect profitability. Understanding these challenges is the first step to overcoming them and ensuring a seamless, efficient warehouse operation.
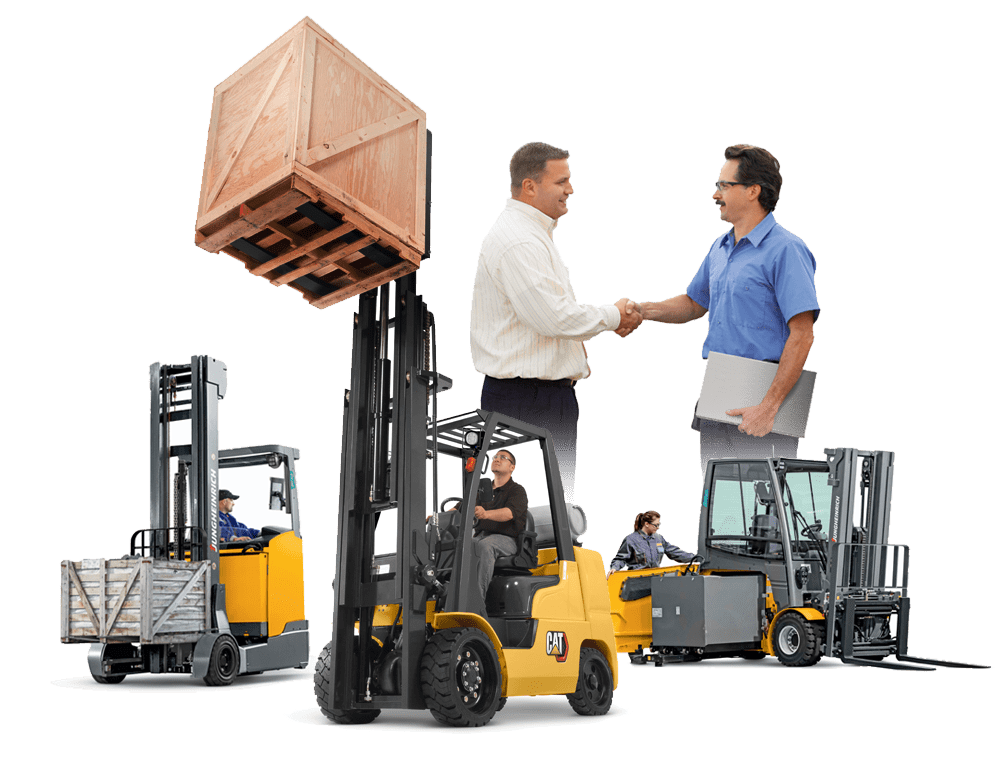
WHAT CHALLENGES ARE YOU FACING?
EQUIPMENT COST & MANAGEMENT
Material handling equipment is expensive to purchase and maintain. Managers need to determine whether to lease or buy equipment and decide how to budget for ongoing maintenance, repairs, and potential upgrades. Rising costs for spare parts, fuel, and maintenance services can further strain budgets.
Tri-Lift NJ is here to make it easy. Our experts will visit your site to fully understand your application and ask targeted questions to identify your specific requirements. We conduct precise measurements and analyze your operational flow, allowing us to design a custom solution tailored to improve your workflow and maximize productivity.
EQUIPMENT UTILIZATION
Ensuring that equipment is used to its full capacity without being overworked is a balancing act. Under-utilized equipment represents wasted investment, while overuse can lead to premature wear and more frequent repairs. Managers need to monitor usage rates and optimize equipment deployment based on demand.
Lift Truck Solutions, also known as LTS®, is your single solution online platform that keeps you connected with your fleet.
This digital fleet-management tool provides you with real-time, actionable data so you can streamline your operations. Lift Truck Solutions allows you to access your equipment, understand your forklifts’ annual usage and track your overall fleet utilization to more effectively run your business. You can also consolidate invoices from multiple locations, request service, repairs or parts and set up monitoring alerts.
MAINTENANCE AND DOWNTIME
Regular maintenance is essential to keep equipment like forklifts running smoothly. However, unscheduled downtime due to breakdowns can disrupt workflows, delay orders, and increase costs. Balancing preventive maintenance schedules with operational demands can be a challenge, especially in busy warehouses.
Relying on a professional material handling service company like Tri-Lift NJ to make sure this service gets done is good business sense.
Maintenance agreements are fixed price programs structured around application and usage, allowing you to better budget your service costs.
OPERATOR TRAINING & SAFETY
Operating MHE requires skill and awareness to prevent accidents. Managers must ensure that staff are trained on equipment safety protocols and handle machines correctly. Inadequate training increases the risk of accidents, injuries, and equipment damage, which can be costly and harmful to productivity.
We offer training at our facility or yours. From a single individual to dozens at a time, we make the training process quick, easy and user friendly; typically, 2-3 hours.
And when it comes to affordability, you’ll find the cost to train surprisingly low!
SPACE CONSTRAINTS
Warehouse layout impacts how efficiently material handling equipment can operate. Tight spaces and poorly optimized layouts can hinder movement and slow down processes. Managers need to configure layouts that allow equipment to operate safely and efficiently, while maximizing available storage space.
It’s common to believe that more warehouse space is needed when there may very well be untapped space within your existing walls. The cost to reconfigure racking for maximum utilization or to design a new warehouse with future growth in mind can be justified when compared to the alternative of adding square footage.
When venturing into the world of warehouse storage, it’s wise to partner with an experienced warehouse professional who knows all the ins and outs of storage design.
TECHNOLOGY INTEGRATION
With the rise of automated and intelligent MHE, such as autonomous forklifts and smart conveyor systems, integrating new technologies into an existing operation can be challenging. Managers must assess compatibility with current systems, ensure proper training for staff, and weigh the upfront costs of new technology against long-term benefits.
Jungheinrich Automated Guided Vehicles (AGVs) are state-of-the-art material handling systems that travel autonomously throughout a warehouse, distribution center, or manufacturing facility, without an onboard operator or driver.
These un-manned vehicles follow a route that has been set out or programmed in advance. They are guided using one of two possible systems: wire-guided systems or laser guided systems. AGVs also facilitate a smooth connection to any host system, such as your preferred Warehouse Management System (WMS) or ERP platform, allowing for an easier and seamless integration into your existing workflow.
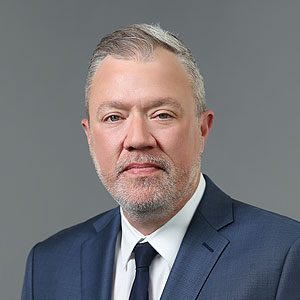
Need Help Overcoming Your Material Handling Challenges? Let’s Talk!
I understand the unique challenges warehouse managers face in maintaining and optimizing their equipment. If you’re dealing with any of these issues—or even something specific to your operation—I’m here to help you find effective solutions. Reach out anytime for expert guidance and support. Together, we can turn these challenges into opportunities for growth!
Chris Dundon
Sales Manager
Cell: 908-421-7760